Autor: Petr Toms
Konstrukce pece
Snad někteří z vás mají ještě v paměti článek s podobným nadpisem, jako je tento. Jen místo šestky stála pětka a také přibylo slůvko „druhé“. Poslední odstavec popisoval všemožné konstrukční změny plánované do budoucna. Dovolím si jej ocitovat v plném znění.
„Ptáte-li se na další vývoj zařízení, pak příští konstrukce jistě nezůstane beze změn. Především upravíme tvar mufle. Předpokládám, že kdyby se směrem dolu zužovala, usnadní se tak propad paliva do prohořených dutin, což přinese rovnoměrnější výkon. Navíc se usnadní manipulace s nádobou uvnitř pouzdra. V této souvislosti vyzkoušíme již zmiňovaný žáruvzdorný materiál Witgert W922. Experimentální provoz jasně ukázal nadbytečnost osazení pro poklop v horní části pláště. Nejen že víko vůbec nebylo potřeba, ale římsa také trochu vadila při hutnění paliva v prostoru mezi muflí a pláštěm.“
Nezbývá než konstatovat, že jen málo ze zamýšlených změn spatřilo světlo světa. Na nové peci chyběla snad jen ta římsa pod horním okrajem. Nepřeskakujme ale, a vezměme to pěkně od začátku.
Zásadním rozdílem obou pecí je naprosto odlišná koncepce. První pec vycházela z dobových záznamů zachycených na dřevorytu z roku 1736. Jedná se o první nám známou zmínku o raku peci, dost možná sahající až k samotnému Chójirovi. Jak jinak začít, než tou úplně první? Ještě než padlo rozhodnutí o výrobě repliky vyobrazené v knize, byl zřejmý jeden významný konstrukční nedostatek. V podstatě se jedná o kónický komín o průměru 40cm a výšce asi půl metru. Zprvu celistvý plášť je svisle rozříznutý na tři stejné díly. I bez velkých zkušeností se dalo předpokládat, že plát s rozměry 50x40x4 cm nemůže bez poškození odolat extrémnímu teplotnímu spádu. Vždyť teplota vnitřku pece dosahovala téměř 1500°C a na nejchladnějším místě vnějšího povrchu by se dala skoro udržet ruka. Rozpraskání kuželu jsme tedy očekávali. Otázkou bylo, na kolik dílů se pec rozpadne a jak rychle. Totální destrukci měla zabránit dvě opatření. Zaprvé už při samotném modelování plátu byla tvořena co možná nejpevnější vnitřní struktura. To by ale samo o sobě nestačilo. Celé těleso obepínají tři silné ocelové dráty, díky nimž drží menší díly pohromadě. Nakonec nás příjemně překvapila odolnost pece. Ti nejoptimističtější z nás předpovídali maximálně dvoudenní životnost. A hle! I po čtyřech dnech pálení a dvou transportech pres celou republiku stále drží. Ale ruku na srdce. Kdo z nás by toužil, mořit se s výrobou nové pece po několika málo vypálených miskách?
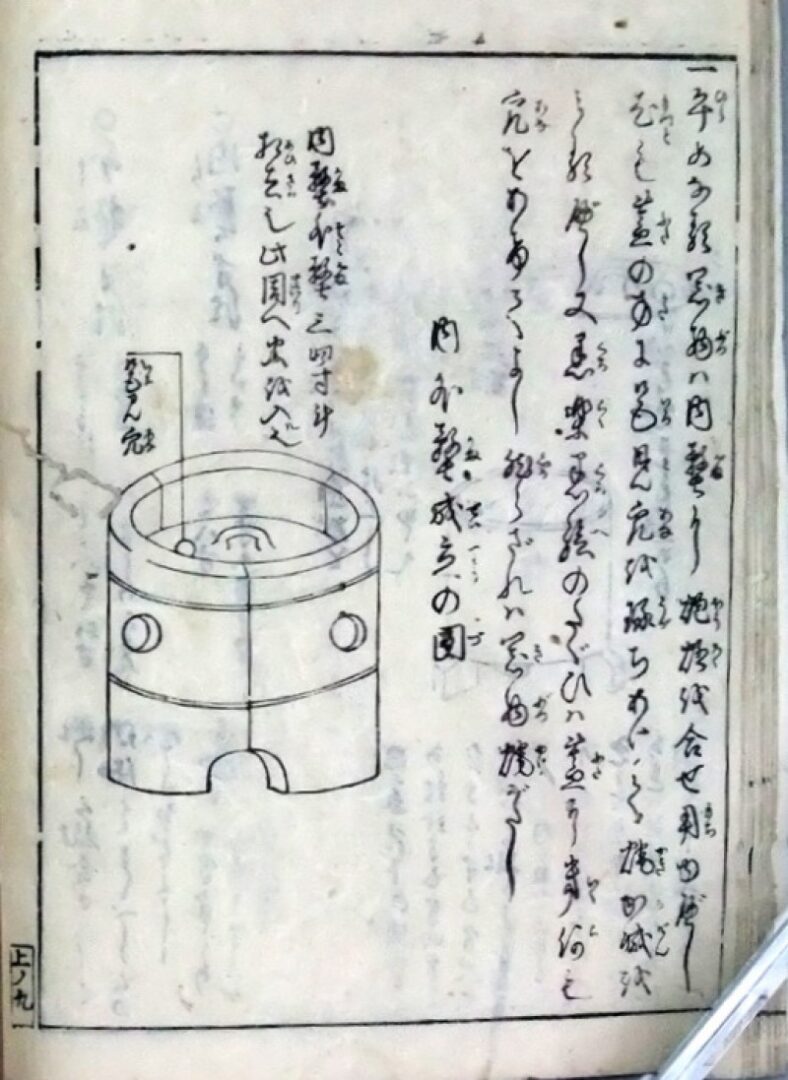

Druhé zařízení již opustilo nostalgii dřevních začátků japonského raku s cílem zlepšit funkci, ale především prodloužit životnost. V drobných náznacích japonského internetu lze objevit další vývojové stupně, vycházející sice tvarem z původní plátové konstrukce, ale mnohem odolnější proti popraskání. Myšlenka je prostá – rozdělit velkou plochu pláště na více drobných částí a rozložit tak vnitřní pnutí na únosnou míru. Kužel se tedy skládá z mnoha pravidelných svislých segmentů. Ty jsou ještě dále horizontálně rozděleny na tři menší díly. Jeden z uživatelů YouTube s nickem „Meiun“ v jednom ze svých mnoha videí o tradičním raku pravděpodobně uvádí, že nápad zmenšit jednotlivé díly pece pochází již z roku 1789. V jeho náčrtku jsou patrné jakési dutiny ve stěně, pravděpodobně zlepšující tepelně izolační schopnosti. Po sestavení a stažení drátem vznikají tři navazující skruže. Vedle razantního snížení vnitřního pnutí získáme další dvě podstatné výhody. Monolit s masivní stěnou, tak jak jsme ji vyrobili my, by vážil okolo 100kg, což by výrazně zkomplikovalo jeho transport. Navíc jednotlivé segmenty k sobě nepojí žádná malta, takže je výměna erozí poškozených kusů záležitostí několika minut. Stačí jen povolit drát.
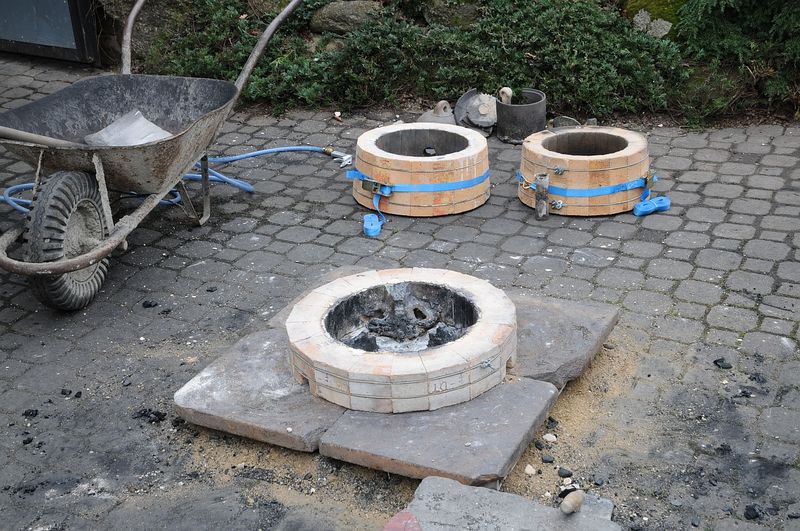
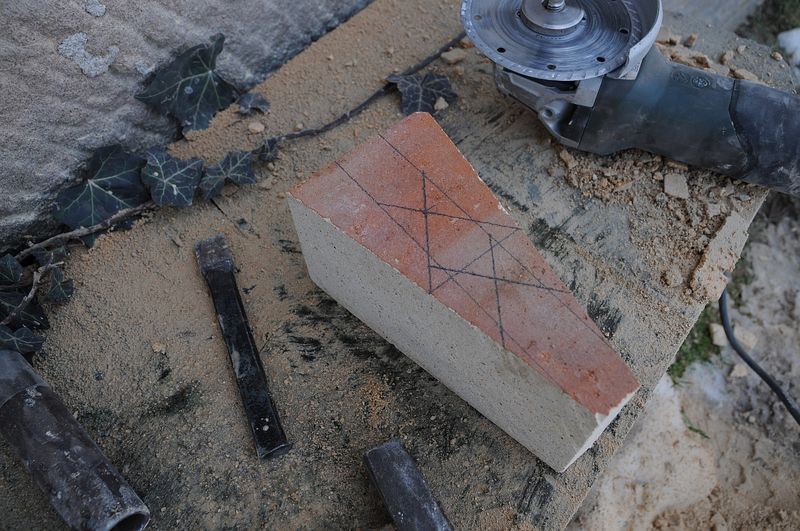
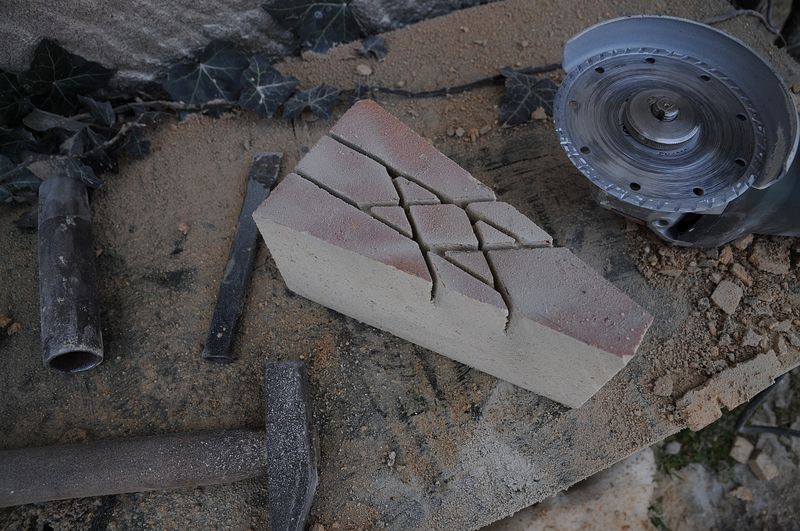
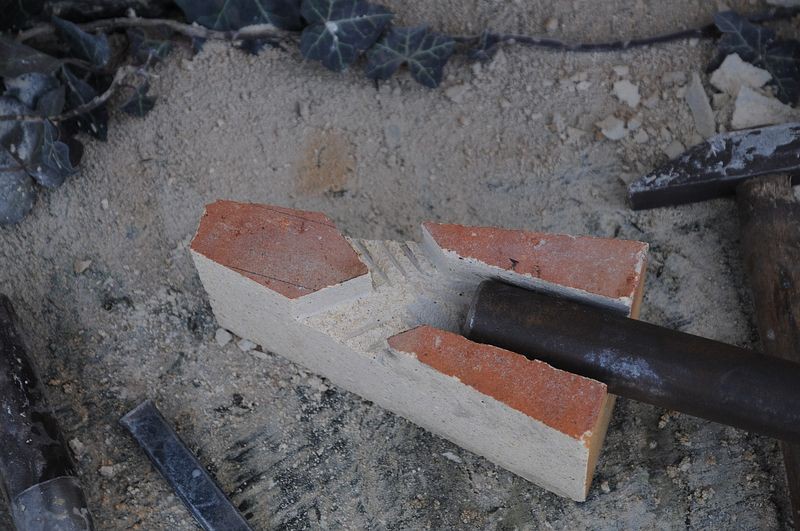
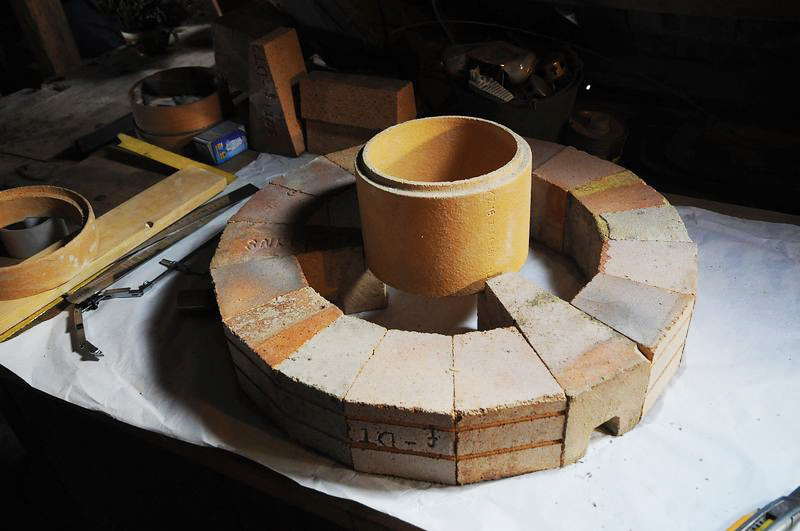
U prototypu z plátů vznikaly potíže se zasekáváním paliva v prostoru mezi muflí a pláštěm. I zde se našlo docela jednoduché řešení. Stačí aby se tento prostor směrem dolu rozšiřoval. Je tedy třeba, směrem ke dnu zužovat mufli, anebo rozšířit pec. Zvolili jsme druhou variantu a postavili pec se strmějším kuželem. Loni se nám z hlediska odolnosti a rychlosti výroby osvědčila mufle uříznutá z šamotové komínové vložky. Její tvar je válcový a nelze jej změnit, a tak rozšíření se pece směrem dolu bylo jedinou možností, jak zlepšit propad dřevěného uhlí.
Před samotnou výrobou pece vyvstala otázka, zda postupovat mokrou, nebo suchou cestou. Jako mokrá cesta je myšleno vtlačování plastické žáruvzdorné hmoty do předem připravených forem. Také lze stejné tvary vytvořit nařezáním hotových šamotových bloků na diamantové stolní pile. Převážily výhody řezání. Správné nastavení pily je sice poměrně zdlouhavé a předchází mu výroba tří různých překližkových šablon, ale řezaný segment je mnohem přesnější, hutnější a odpadá pálení na vysokou teplotu. Jako polotovar posloužily různé formáty žáruvzdorných tvarovek z jakostních šamotů značky STV1. Jejich výhody tkví ve zvýšené odolnosti proti erozi za vysokých teplot a přesný tvar a rozměry. Dříve než se rozezvučel diamantový kotouč, bylo zapotřebí sáhnout hluboko do paměti, vylovit něco ze základů deskriptivní geometrie a zkonstruovat technický výkres, respektive odvodit všechny rozměry a úhly požadovaných segmentů.
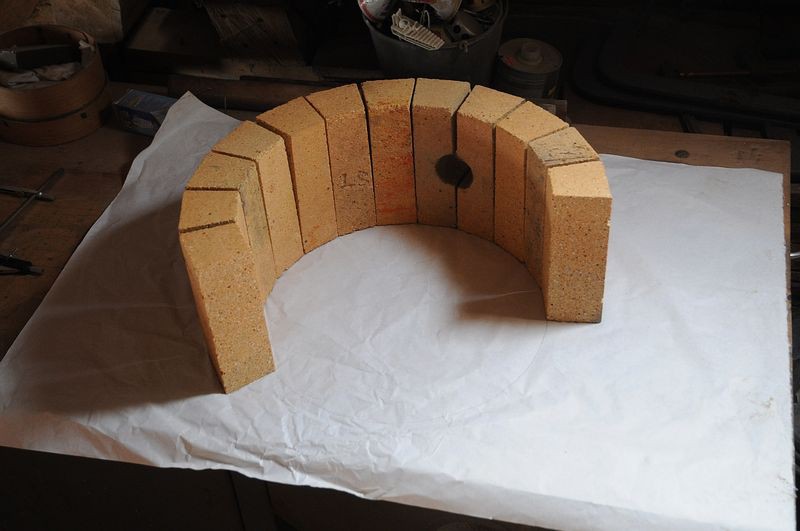
Samotná mufle zůstala téměř beze změny. Detaily její skladby najdete v loňském článku o peci z plátů.
Pozorný čtenář si možná klade otázku „Téměř beze změny znamená, že je přeci jen něco jinak?“ Ano, bez předchozího záměru jsme oslovili výrobce komínových vložek firmu Schiedel. Velice zajímavá se zdála být nabídka vložky 33 ADV 16 vyráběná isostatickým lisováním do forem. Se svou 6 milimetrovou stěnou slibovala nesmírně efektivní prostup tepla. Potíž však nastala při vrtání otvoru pro kukr. Běžnou šamotovou vložku lze vrtat speciálními tvrdokovovými vrtáky na sklo a keramiku, ale v tomto případě by se více hodil nějaký diamantový nástroj. Provrtání stěny zabralo asi desetinásobek času, než u běžného materiálu a kvůli častému broušení byl na jednom otvoru spotřebován jeden celý vrták.
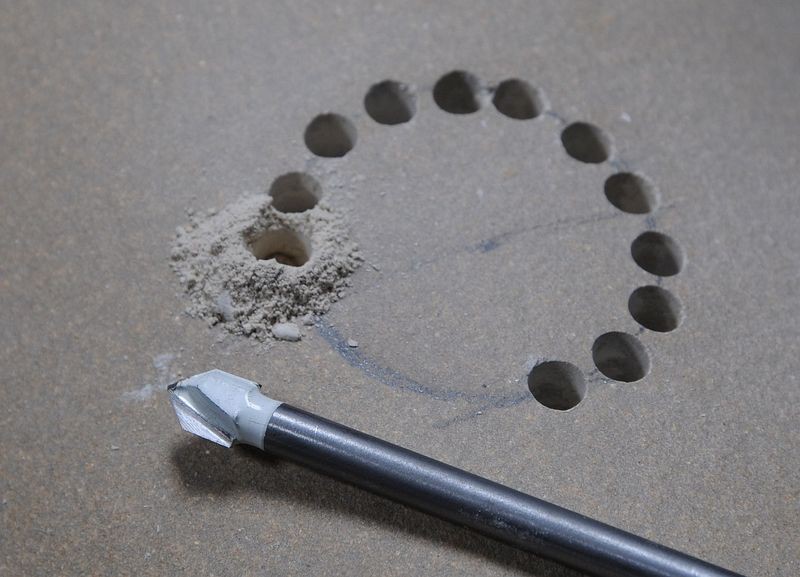
O měchu jako zdroji stlačeného vzduchu jsme už na ARTkeramice také psali http://www.artkeramika.cz/cernoraku-2016-prvni-vyuziti-mechu.
Největší obava v tomto ohledu vycházela z potenciálně nedostatečného výkonu ručního dmýchání. Také tu hrozilo nebezpečí prasknutí pláště horního měchu. Ponechali jsme totiž tuto část původní a na první pohled bylo zřejmé, že sto padesát let stará zteřelá kůže nemusí zvládnout tak náhlé probuzení. Rozvodné hadice se minule osvědčily, takže nedoznaly žádné změny. Drobnou úpravu konstrukce bylo třeba provést na rozvaděči. U pecí na dřevěné uhlí je nezbytné, regulovat průtok vzduchu. V případě foukání ventilátorem postačilo zahradit hrdlo sání. U měchu toto nebylo možné a proto jsme vsadili posuvnou klapku přímo do tělesa rozvaděče.
Funkce pece
Největší obavy o správný chod přirozeně panovaly před první akcí, ale i letos provázelo přípravy množství otázek. Největší neznámou představoval měch. Možný nedostatek výkonu a s tím spojené problémy s dosažením potřebné teploty zaměstnávaly laboratoř a glazovnu. Potencionálně nízkou teplotu jsme museli kompenzovat zařazením vhodných taviv do kompozic glazur. Praxe však ukázala, že měch v mnoha ohledech i předčí elektrický ventilátor. Nejen že výkon historického stroje naprosto dostačoval, ale ruční dmýchání navíc umožňuje citlivě reagovat na měnící se odpor odhořívajícího uhlí v peci a také jím lze pružně měnit výkon v závislosti na požadované rychlosti nárůstu teploty. Také nebylo předem jasné, kolik lidských životů spotřebuje neustálé tahání za páku měchu. Nevedli jsme sice žádné přesné statistiky, leč můžeme odhadnout průměrnou výdrž jednoho otroka zhruba na ½ hodiny. Samozřejmě vše velmi záleží na fyzické a psychické kondici každého jednotlivce. Ze strachu o gumové přívodní hadice bylo nutné mírně foukat i při výměně misek v pouzdře. Původní horní díl sloužící jako zásobník stlačeného vzduchu respektive jeho kožený plášť, i po padesáti letech odpočinku zvládl nástup do služby bez sebemenších potíží.
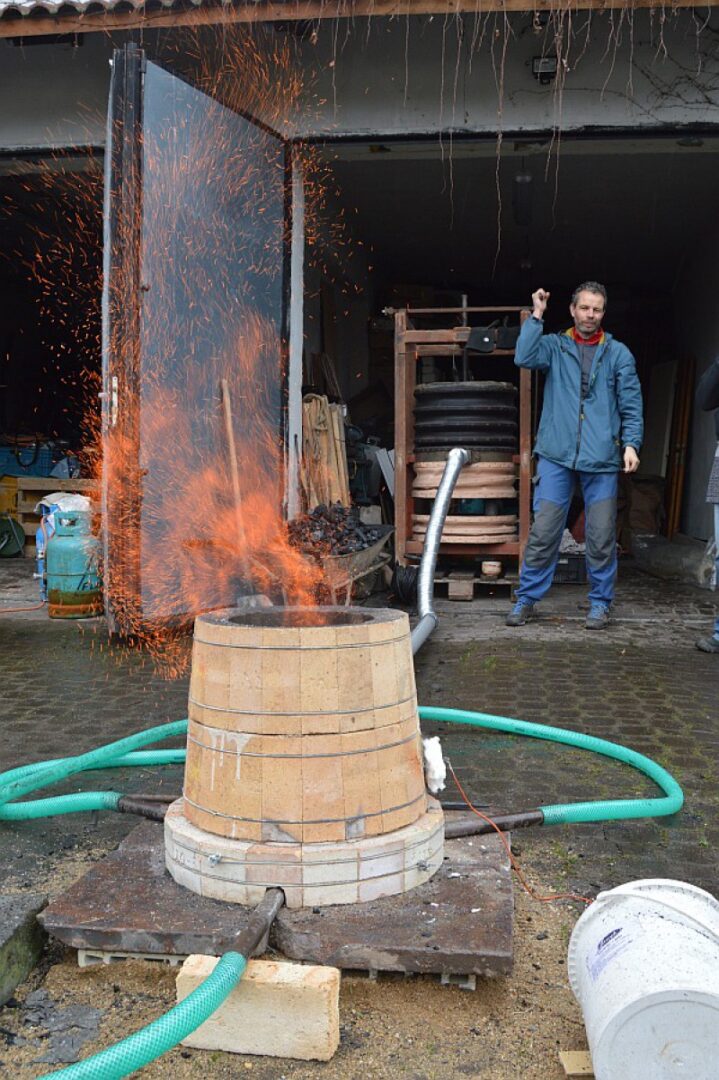
Samotná pec pracovala na jedničku. Ani větší akumulace tepla zdivem nijak neovlivnila růst teploty. Po třech celodenních směnách vyzdívka ani na jednom místě nepraskla. Na základě loňských zkušeností se spékáním pouzder, den, kukrů a dyzen jsme bezprostředně po vytažení poslední misky celé směny rozebrali vnitřní struktury, dokud byly popelové nánosy měkké. Čištění vnitřku pece od popele a nánosů strusky tak bylo oproštěno od hrubého rozbíjení saggaru. V podstatě jde jen o zmírnění násilí, protože ani ta nejodolnější komínová vložky nezvládne vzdorovat odtavování tekutými popely déle než jednu směnu. Podobně trpí i dyzny vedoucí spalovací vzduch do nitra rozžhaveného paliva. Vyzdívka samotné pece na nejteplejších místech jistě vydrží alespoň dvacet směn.
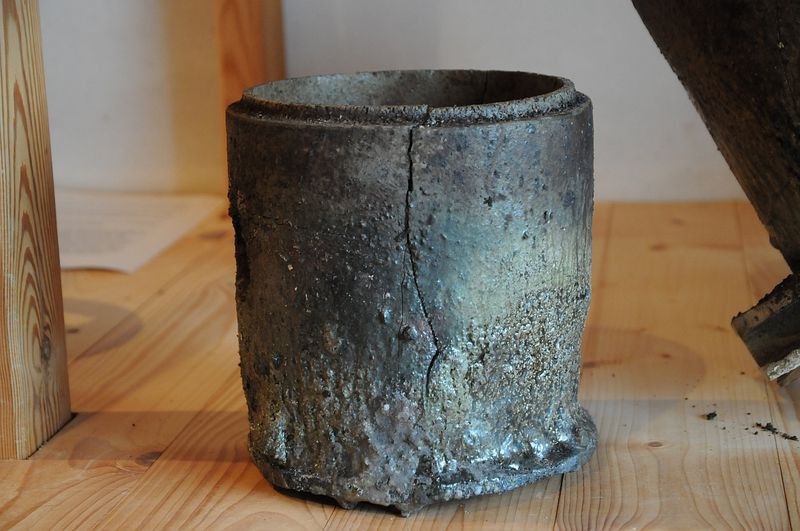
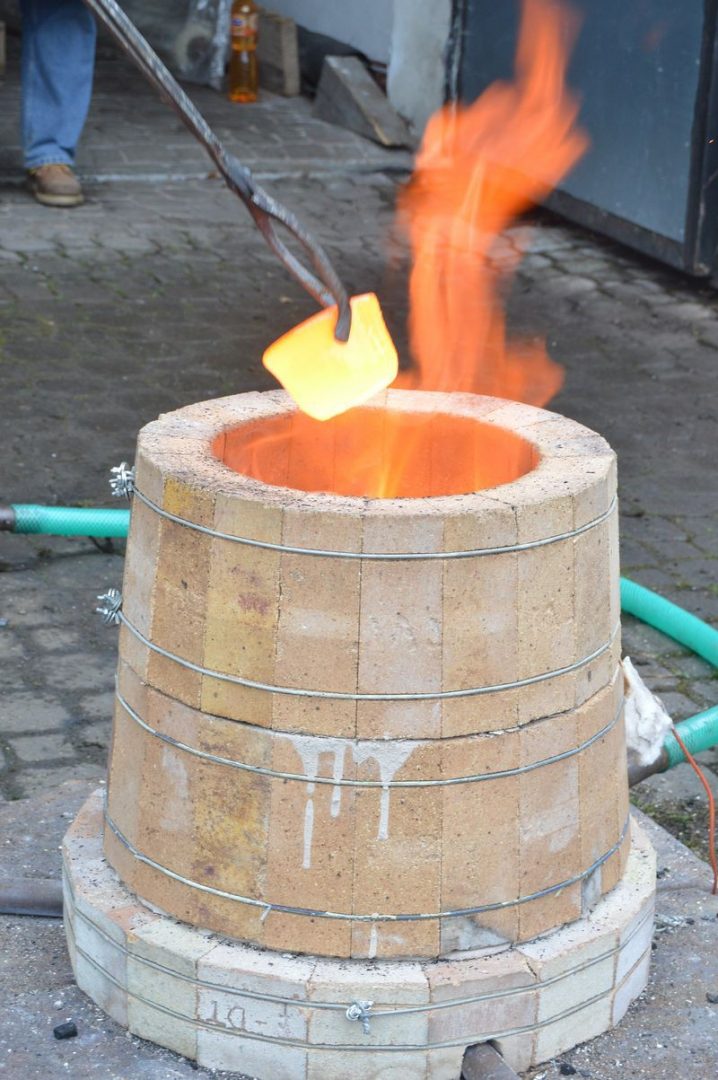
Na semináři podstoupili materiálový test mimo jiné i pokličky uzavírající pouzdro. Sledovali jsme odolnost německé hmoty Witgert 922 a šamot SN1 z Velkých Opatovic. Navzdory očekávání déle vydržela česká hmota.
Pokud bychom měli porovnat novou segmentovou konstrukci poháněnou měchem a plátovou pec osazenou ventilátorem z hlediska dosahovaných teplot, lze konstatovat, že jsou obě zařízení srovnatelná. Ohřev pece z nuly na provozní teplotu zabere asi 1 hodinu. Běžně dosahovaná teplota v pouzdře činí 1270°C. Jeden pálící cyklus trvá přibližně 12 minut, nicméně bylo možné misku vypálit i za poloviční dobu. Takto rychlý nárůst teplot by nádoby nevydržely. Předehřívali jsme je tedy v plynové peci na cca 700°C.
Chystané konstrukční změny
Snad to nebude znít příliš nabubřele, když řeknu, že se nová pec kromě několika drobností skvěle osvědčila a většinu potíží plátové konstrukce se podařilo odstranit. Asi nejdůležitější námět na změnu lze spatřovat v úpravě hrotů dyzen vyčnívajících do spalovacího prostoru. Celá tryska je prozatím neoddělitelnou součástí nejspodnějšího cihlového prstence. Výstupek podpírající pouzdro velmi trpí odtavováním. Každá výměna celé dyzny znamená rozebrání podezdívky. Pokud by se podařilo dyznu rozdělit na dva díly, umožnilo by to výměnu pouze té části, která je exponovaná ve spalovacím prostoru a zbytek může trvale zůstat součástí zdiva. Jistě by nebylo od věci použít pro výměnnou část kvalitnější materiál. Lze se domnívat, že by dobře posloužil vysoce hlinitý šamot.
Další úpravou by mohlo být nahrazení zelených zahradních hadic něčím, co by snáze odolávalo teplu a jiskrám a zároveň lépe vypadalo. Současná podoba hadic také zvyšuje riziko zakopnutí a pádu.
Přestože historický měch zrestaurovaný do stavu plné funkčnosti pracoval na 110%, uvažujeme o jeho náhradě. Rádi bychom vytvořili repliku krabicového pístového měchu fuigo. Jednak se ještě více přiblížíme původnímu vybavení, ale především ušetříme náročný transport ohromného kolosu z rakousko-uherských kováren. Pokud by někdo s vás náhodou disponoval kožešinou psíka mývalovitého, rádi jí odkoupíme a v souladu s tradiční technologií, použijeme jako těsnění pístu.
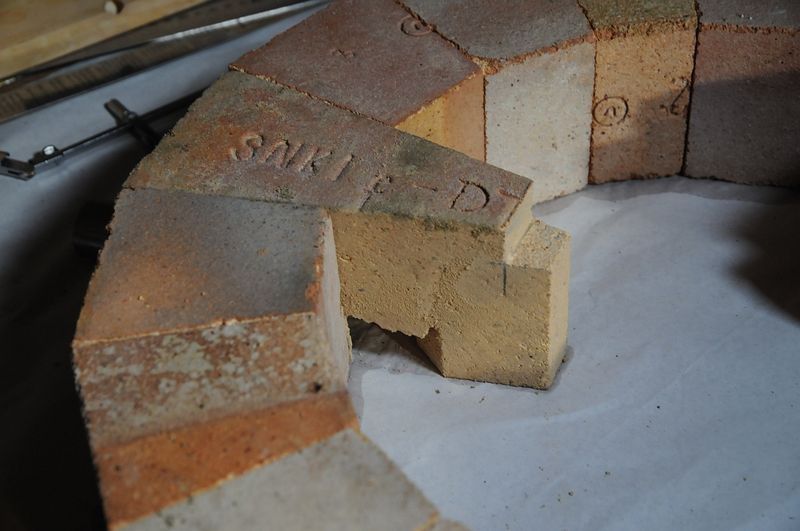
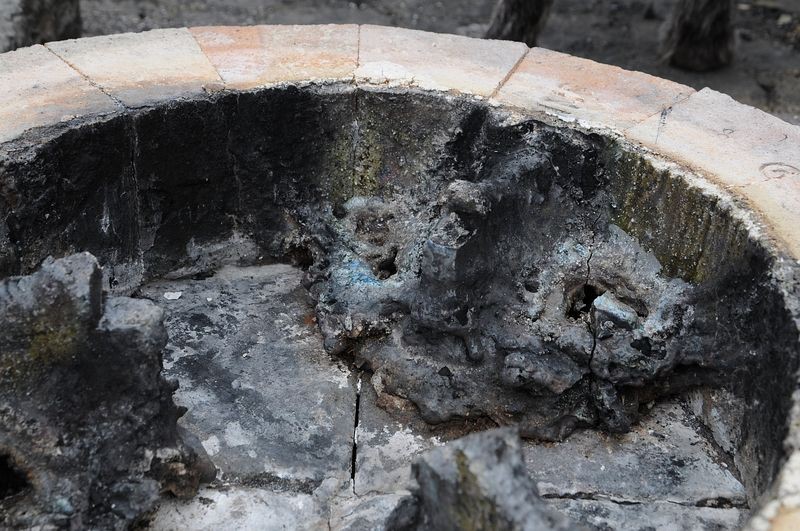
Dílčí konstrukční úspěchy postupně přibližují námi vyvíjené pece na dřevěné uhlí ke každodennímu využití a to i vysoko nad rámec techniky kuro raku. Těžko překonatelnou devizou je nevídaná flexibilita, díky níž lze v jedné hodině vypálit čtyři naprosto odlišné výrobky. Snad nejdůležitější přidanou hodnotu spatřuji v možnosti nezprostředkované a kreativní práce s jedním z živlů – s ohněm.
Mnoho štěstí při stavbě pece na dřevěné uhlí přeje všem pecařům a paličům
Petr Toms
Vedoucí pracoviště „Segmentová pec s měchem“ na semináři Černoraku 2016